Offset part of the offset press (1)
3 Ink section
Water and ink are the conditions on which the quality of prints depends. The best balance between ink and ink can ensure the reproduction of prints, color reproduction, and good clarity. Once the balance of water and ink is destroyed, a series of printing failures will occur. It is very important to grasp the balance between water and ink, but it is also the most difficult. In the printing presses, there are special water supply and ink supply agencies. Their working conditions have a direct impact on the ink-water balance. Correctly understanding and mastering the working principles of the ink-and-ink mechanism has a positive significance for the realization of ink-water balance.
3.1 Inking mechanism
The function of the inking mechanism is to supply the ink uniformly, stably, and continuously to the surface of the printing plate. The ink transfer mechanism is composed of several parts of ink fountain and ink fountain roller, ink transfer roller, ink fountain roller, uniform ink roller, heavy roller, ink roller and ink roller. The following is a detailed analysis of the role and working principle of each part.
1. Ink fountain and ink fountain roller. The role of ink fountain is to hold ink. The role of the ink fountain roller is to take out the ink inside the ink fountain and transfer it forward. The action of the ink fountain and the roller roller is interdependent and cannot leave one side alone, as shown in Figure 3.1.
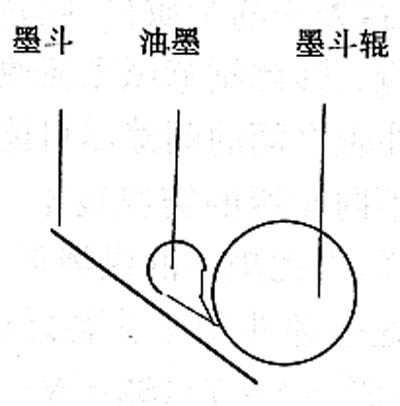
The ink is actually stored in the groove between the ink fountain and the ink fountain roller, and the ink transfer of the ink fountain roller is performed through the gap between the ink fountain roller and the ink fountain.
The overall function of the ink fountain and the ink fountain roller is to supply ink to the subsequent ink path. The amount of ink supply is determined by the distribution of the graphics on the surface of the print. So how to control the size of the ink at the ink fountain roller? According to the diagram, it can be seen that the amount of ink output is related to the gap between the ink fountain and the ink fountain roller. The larger the gap, the greater the amount of ink discharged; the amount of ink discharged is also related to the rotation angle of the ink fountain roller, and the larger the rotation angle is, the more The larger the amount of ink, the ink amount is assumed to be represented by S, the gap between the ink fountain and the ink fountain roller is represented by T, and the rotation angle of the ink fountain is indicated by A, then S=A×T. When the ink discharge amount is insufficient, the A value or the T value can be increased; when the ink discharge amount is excessive, the A value or the T value can be reduced. When the ink output is constant, A and T are inversely proportional, that is, A increases, T decreases or A decreases, T increases to ensure the normal amount of ink. In normal printing, the amount of ink discharged S is not allowed to change, that is, the product of A and T is a constant.
Can A and T be chosen arbitrarily based on their inverse relationship? From the perspective of uniform ink, the thinner the ink layer, the better the effect of uniform ink; from the perspective of ink separation, the thinner the ink, the better the separation effect; from the perspective of ink supply control, the thinner the ink, the control The more sensitive it is. Therefore, in a word, try to make the ink thinnest. Changing the thickness of the ink layer can only adjust T, that is, the gap between the ink fountain and the ink fountain roller. The adjustment can be made by the following top wire. When the value of T decreases, the value of A must be increased to ensure the ink supply. Therefore, the adjustment principle of the ink fountain and the ink fountain roller is:
a. The smaller the gap between the ink fountain and the ink fountain roller, the better;
b. The larger the corner of the ink fountain roller, the better.
The decrease in the gap between the ink fountain and the ink fountain roller is limited, and the smaller the ink is, the more difficult it is to perform. After the size, the impurities of the ink fountain can easily block the ink, and the increase of the rotation angle of the ink fountain roller is also limited. Therefore, the principle of adjustment should be changed to: Under the condition of ensuring sufficient ink supply, the gap between the ink fountain and the ink fountain roller should be as small as possible, and the rotation angle of the ink fountain roller should be as large as possible.
The amount of ink needed for different printing plates is different, and the amount of ink needed for different positions of the same printing plate is also different. Therefore, the ink supply volume of ink fountains must be adjustable in the axial direction. This adjustment is mainly achieved by different gaps between the ink fountain and the ink fountain roller at different positions, ie, S1=A·T1, S2=A·T2,.........Sn=A·Tn. Use a small A value, that is, a small ink fountain roller rotation angle, and adjust T1, T2, ..., Tn, and then increase the A value to achieve the desired ink supply. If a larger value of A (ie, a larger angle) is used at the beginning, the amount of under ink will be excessive, and it is troublesome to remove these excessive ink amounts.
For places where no ink is needed, ie, S=0, how do you tune it? Since the A values ​​are common, only the T value can be reduced to zero. It is difficult to strictly reduce the value of T to zero. Inadvertently, the ink fountain and the ink fountain roller will erroneously and scratch the surface of the ink fountain roller. Therefore, the T value cannot be reduced to zero here, but only slightly larger than the zero value. There is a little ink on the ink fountain roller. The film can, this layer of ink film can actually play a role in lubrication. The rotation of the ink fountain roller is driven by a set of linkage mechanisms. However, the tensile strength of the connecting rod is limited after all. If the value of T becomes negative, one or both of the connecting rod and the ink fountain roller must be damaged. Indentation is generally left in the circumferential direction of the ink fountain roller.
2. Ink roller. The function of the transfer roller is to transfer the ink on the ink roller to the ink roller (or roller). Since the ink layer on the ink fountain roller is unevenly distributed along the axis, this brings great difficulties for ink transfer. The thicker the ink film, the worse the uniformity. Therefore, from the viewpoint of ink transfer, the ink film of the ink fountain roller is also required to be as thin as possible. The ink transfer roller must take care of each part when transmitting ink. This can only be achieved by increasing the contact pressure. The pressure between the ink transfer roller and the ink fountain roller is controlled by the spring and can be adjusted by the size of the spring force. To change the pressure. However, the pressure should not be too great, and the impact will be formed at the moment of contact with the ink fountain roller. The pressure between the ink transfer roller and the ink roller can also be adjusted, but it must be noted that the pressure should be as uniform as possible in order to even out the ink.
Cup & Mug Pot & Kettle Co., Ltd. , http://www.nscupmug.com