Offset printing press role and adjustment (a)
2.7 Printing pressure
2.7.1 The role of printing pressure
1. Make up for machine processing errors. This is a very important role for printing pressure. If there is no printing pressure, due to the processing and installation errors of the machine, it is impossible to completely contact the surfaces of the two rollers, and the uniform transfer of the ink cannot be guaranteed. There are unevenness errors on blankets, plate surfaces, and paper. These errors must also be eliminated, so the printing pressure is also a reflection of the machine's accuracy.
2. Transfer ink. The use of printing pressure is to transfer ink so that printing can be completed. Through experimental analysis, the relationship between printing pressure and ink is similar to the following:
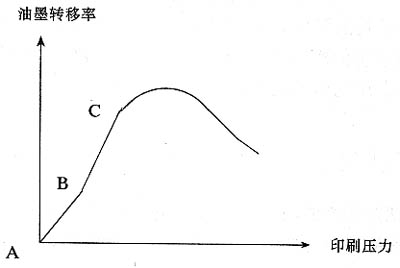
AB segment to compensate for the overall error of the machine, BC ink into the normal transfer stage, after C point, the pressure increases, the ink transfer not only did not rise, but decreased, so the printing pressure must be controlled within the BC segment, in this The transfer amount and pressure of the segment ink are basically linear.
3. Get good printability of paper and ink. The shape of the ink transferred to the paper has a very close relationship with the printing pressure. Large pressure, large deformation of the ink, and easy to paste version, but the permeability is good, the pressure is small, ink scars, poor permeability. Changes in paper or ink changes require re-selection of printing pressure. The best printing pressure.
2.7.2 Principle of formation of printing pressure
Printing pressure is reflected in the amount of contact surface compression. In general, the amount of deformation of the rigid roller is negligible compared to the amount of deformation of the lining, so the printing pressure P is usually expressed by the amount of deformation of the lining:
P=E·L (E is elastic modulus, L is compression)
From the above equation, it can be seen that the printing pressure is in formal relationship with the material's performance and the amount of deformation during compression. Therefore, the same amount of deformation, the lining of different materials, the printing pressure is not the same, there are similar problems with the paper. Therefore, the value of the pressure measured by the fuse can only be used as a reference. In the end, it is suitable for specific analysis. There is a deformation amount (that is, at the printing pressure). The rollers cannot be line contact but only surface contact. The distribution of the printing pressure on the contact surface is calculated roughly as shown in Fig. 2.10b.
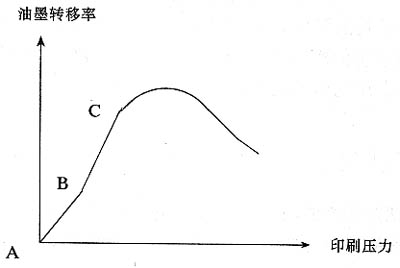
The pressure of the centerline of the contact surface is the largest, and the pressures on both sides of the centerline decrease in turn. This is because the deformation on both sides is smaller than that in the middle, and the pressure in the middle of the drum is smaller than the pressure on both ends. This is mainly because there is bending deformation when the drum is running. as the picture shows. The smaller the bending, the more uniform the pressure. The size of the bend is inseparable from the material's own properties, processing and installation accuracy, and printing pressure. To reduce the bending, it is only possible to increase the rigidity of the roller, improve the precision of machining and installation, and reduce the printing pressure.
The distribution of the printing pressure is symmetrical in the middle section, so that it is preferable that the print product be kept in sync with this symmetrical relationship, that is, symmetrically distributed in the same intermediate section.
Leather Watch,Women Watch,Ceramic Watch
Lovers Couple Watch,Quarts Watches Co., Ltd. , http://www.chleatherwatch.com