Prepress processing of label prints
In recent years, the competition in the label market has become increasingly fierce, and the requirements of users for label printing quality have been continuously improved. At the same time, the use of narrow-width flexographic printing technology not only expands the company's business scope and production capacity, but also prepress processing and media. The selection, screen production and flexographic printing technologies have also accumulated rich experience.
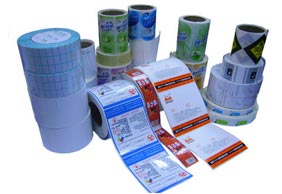
First of all, in terms of prepress processing, many customers design orders based on offset or gravure printing. If this type of manuscript is printed on flexographic printing, proofs will have many quality problems. For example, the color is not in place and the level is not obvious. There are hard edges and so on. Therefore, to solve such problems, it is necessary to communicate with customers in a timely manner.
Second, we must also shop around in the selection of flexible plates. Printing companies need to cooperate fully with several plate-making companies to fully understand issues such as the use of plate materials, the production of cable screens, the transition of levels, the increase in compensation for outlets, and the rate of plate retraction. This not only facilitates production, but also controls quality parameters, avoids human interference, and reduces the occurrence of failures.
Again, because of the special nature of label printing, narrow-format flexographic printing equipment has prominent features with respect to embossing and other types of flexographic printing equipment. The narrow-width flexographic printing equipment is not only simple in operation, but also has high printing quality and operating efficiency. Strong combination, can do more kinds of products, more competitive strength.
1. Selection of color sequence
Flexographic printing of the label part of its graphics mainly on the ground, lines, text-based, used in the printing materials are mostly paper, aluminum foil, plastic film, stickers and so on. When water-soluble or solvent-based inks are used to print the absorbing printing materials, after the infrared hot air drying effect occurs, the materials will be pulled up and affect the overlay accuracy. Color plates containing large areas should be printed in the rear cell because the substrate is infrared dried after absorbing a large amount of ink, and the field cell's pull-in change is larger than that of other cells. If it is necessary to place the field part in the front color group, it is sensible to increase the compensation in the up and down direction to make up for the loss caused by the soaring of the printing material.
2. Note on plate making
(1) Trapping
When making flexo, a certain amount of trapping facilitates print registration. Trapping too small or not trapping will result in misregistration (darkness) in the printing. Trapping over a large outline on the edge of the print will affect the overall effect of the label.
(2) layout design
Since flexo printing basically uses web printing, the application of seamless sleeve technology greatly saves paper, but some flexographic printers cannot achieve on-line die-cutting, but also require subsequent processing (cutting, etc.), so the The layout is fully considered to leave sufficient margin for subsequent processing.
(3) Selection of raw and auxiliary materials
The choice should not be limited to the unit price, but the printing quality should be taken as the first element. The product cost should be analyzed. The raw and auxiliary materials that need to be considered are mainly paper and ink.
Cold Storage Board,Cold Room Panel,Pu Sandwich Panel
Polyurethane Insulated Panel Cold Storage Room Co.,Ltd , http://www.nscoldroomstorage.com