Color printing overprint accuracy
First, the factors that affect the accuracy of overprinting There are many factors that affect overprinting accuracy. In addition to the film errors caused by the factors of platemaking, several major aspects of printing are described as follows:
1. Influence of Printing Plate on Overlay Accuracy Lithographic printing plates are mostly thin and light aluminum. During the printing process, the overprint accuracy is affected by changes in its shape or volume.
The deformation of the printing plate is generally caused by two aspects. The first is stretching and deformation, and the second is baking deformation. Stretch deformation means that during the school printing process, due to the operator's improper use of force during plate loading and printing, artificially causing the metal plate to extend (stretch) in the circumferential direction of the platen, resulting in overprinting of the plate graphic and text. Baking deformation refers to the change in the linear dimension of the printing plate due to improper baking when the baking is performed in order to improve the printing resistance of the dried PS plate. As we all know, most of the metals have the characteristic of thermal expansion. When the printing plate is heated to 250 degrees Celsius in the oven, the plate base will be baked softly, affecting the stability of the layout size. The uneven temperature in the oven or overbaking is particularly serious, and it can cause scrappage in severe cases.
2. The effect of the roller lining on the overprint accuracy can ensure that the linear speeds of the printing plate, the eraser, and the embossing 3 roller are consistent, so that the transfer can be effectively performed under a certain pressure. If the plate cylinder liner is too thick, the radius of the cylinder increases accordingly. With the same angular velocity, the linear speed of the drum surface with an increased radius will increase. The resulting speed difference will not only cause the printing plate to wear, but also cause the size of the layout image to be “compressed†in the front-rear direction. The drum liner is too thin and the radius is reduced accordingly. The linear speed of the drum surface will be slow, and the dots will be stretched during the transfer process, which will cause the graphic area to “magnifyâ€, resulting in inaccurate overprinting. In the two-color machine, this phenomenon is particularly apparent.
3. Influence of paper on overprint accuracy In offset printing, the paper that has a greater impact on overprinting is paper, especially offset paper. This type of overprint due to paper is not easy to control.
The composition of paper is mainly fiber. The characteristics of fibers are water swelling and syneresis. In the offset printing process, when the first color is printed and then the second color is set, the overprint due to the retraction of the paper is inaccurate. Paper structure has high strength, good smoothness, thick coating, and low water absorption. It is particularly serious for some papers with loose structure, light sizing and strong water absorption.
The paper's stretching deformation is affected by the temperature and humidity of the surrounding environment. In the printing process, it is also squeezed by the roller. Squeeze causes the paper to extend outward from the mouth of the mouth and extend to the edges of the tip. The overprint error is greater. This phenomenon is often referred to as "sweep angle."
4. Influence of mechanical aspects on overprinting The printed paper must be effectively controlled by the mechanical components from the beginning to the end of the machine, and the relative position must be stable during the transfer and transfer process. Only in this way can the requirements for overprinting accuracy be met, otherwise overprinting accuracy will be greatly affected. The most influential factors are the following: First, the paper positioning, that is, the problem of the mechanical parts of the rules caused by overprinting is not allowed; Second, the paper is in the transfer and transfer process, due to the transfer of instability, resulting in changes in the relative position of the paper caused Imprinting is not allowed.
In addition, when the paper is peeled off from the drum, it is subjected to adhesion force and peeling tension. If the gripping force cannot overcome the peeling force, paper whip occurs and a small displacement occurs. This type of image appears to be misprinted on a stand-alone machine, and appears as a ghost image on a multi-color machine.
Second, the overprint accuracy control method For the impact of overprinting accuracy factors, take the appropriate control methods to achieve the purpose of overprinting accuracy.
1, the baking of the printing plate must be done in the oven temperature...
It is necessary to standardize the operation of the school edition. The layout of the plate is centered, the plate is mounted on the plate, and the plate screws are fastened. When pulling the plate, tighten the top screw. As long as the force is moderate, deformation of the plate is generally avoided.
2. The distance between the centers of the rollers is strictly measured according to the standard, and it must be done that the roller axis lines are horizontal to each other and the lining calculation is accurate. After a good lining, do a stress test. Generally, the methods of “playing screensâ€, “drawing mapsâ€, and “pressure bars†are adopted to ensure “flat pressure†to meet the printing accuracy requirements.
3. It is difficult to solve the impact of paper on overprint accuracy, and there are many related factors. In order to improve the printability of the paper and enhance its stability, the temperature and humidity of the printing environment should be kept relatively constant. At the same time, according to the "hysteresis effect" of the paper, the prepress processing of the paper is accomplished. The commonly used method is hanging and the paper is hung by hanging, so that the moisture content of the paper is relatively balanced with the air humidity, which can reduce the sensitivity of the paper to the environment.
For the high-precision prints, it is also possible to use the method of first printing the paper with water once, so that the paper can absorb water and pressure sufficiently, allowing the paper to form before the overprint. In this way, the "slew angle" and the expansion effect are all higher than those of Zou, but the cost is higher.
4, printing process requirements, in the case of guaranteeing non-dry version, use the smallest water.
5, mechanical overprint is not allowed, mainly the rules of the parts of the decayed teeth. The requirements for the front gauge are: According to the thickness of the paper, the height position is correctly adjusted, and the line connecting the front regulation paper points is parallel to the axis of the drum; the requirements for the pull vision are: reliable paper drawing. Each paper and paper feeder must ensure that the paper runs straight. The grippers must be uniform in strength, close and open accurately, and when the two teeth transfer the paper, there must be enough time for mutual success to ensure effective control of the paper. In addition, the rollers and the shaft must be free from turbulence.
Satisfying the above requirements, under normal circumstances can improve the accuracy of overprint to achieve control purposes.
High temperature Bulk Bag is a special kind of Jumbo Bags. Ordinary jumbo bags usually can only bear the temperature of 80 degrees Celsius, more than the temperature, the jumbo bags parameters obviously happens, bearing capacity is affected by temperature plummeted, cause a breakage of the bags, cannot use.But just came out from the machine in the production of many products often have a relatively high temperature,80° the limit temperature can not meet the requirements of this product. so a lot of products have to choose high cost of steel drum to pack, Not only is it bad for loading and unloading, but it also adds a lot of cost. Our company research and development of high temperature resistance bag can be very good to help clients to solve the problem. Under the temperature of 130 degrees Celsius, and to ensure that the high temperature bulk bag not obvious changes in various parameters, is not affected by temperature and reduce the bearing capacity ,effective help customers achieve container unitization transportation, greatly saves the cost, we are professional do jumbo bags ,Fibc Bags ,Plastic Woven Bags suppliers in China, welcome to contact us, looking forward to cooperating with you
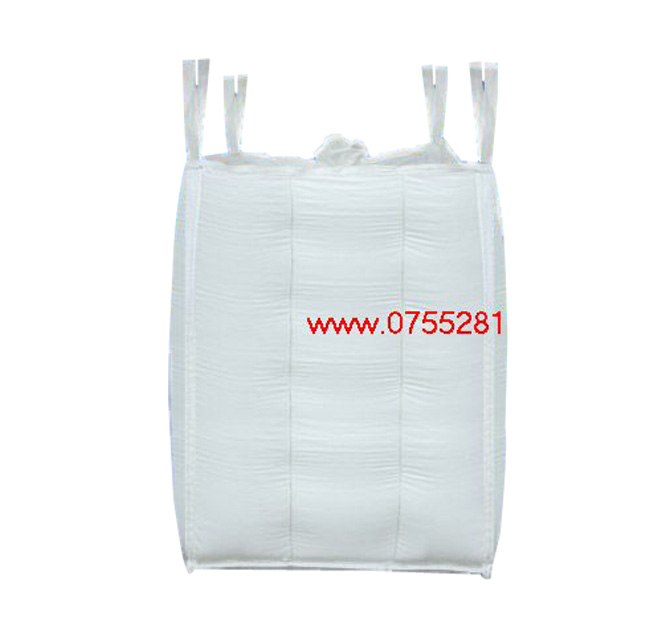
High Temperature Bulk Bags,Big Container Jumbo Bag,Bag For High Filling Temperature,High Temperature Roasting Bag
Shenzhen Riversky Packing Materials CO.,LTD , http://www.jtfibc.com