Technical terms for microbalances
readability
The readability of the balance refers to the smallest difference between the two weighing values ​​that can be read on the display. When using a digital display, this refers to the smallest numerical increment, also known as the "dividing value".
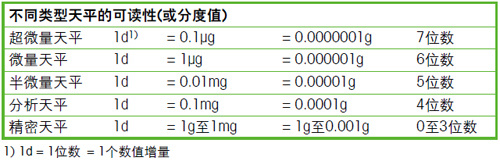
Note: "DeltaRange" and "DualRange" balances have two different types of readability and have a high cost performance.
Accuracy
The definition of whether the test result can be corrected or approximated to the reference value is in accordance with the definition or agreement [DIN1) 55350-13]. Or in short: the display value of the balance is close to the actual quality of the sample.
Test weight accuracy level
Summarize different weights of the same accuracy level. It is recommended that the weight classes classified according to OIML2) R111 ensure compliance with the error limits for weight classification and ensure that the surface quality is consistent with this international recommendation. As the control part of testing, weighing and testing equipment, quality management standards require the use of traceable weights to calibrate or adjust the balance at an appropriate cycle. The weights used for this purpose must be certified with a corresponding level of accuracy.
Indication error
The change value of the output variable of the weighing instrument is divided by the change value of the related input variable ([VIM] 5.10) 1). For the balance, it is the change value of the weighing value ΔW divided by the load variable Δm
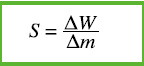
Indication error is one of the most important technical parameters of the balance. The indication error specified by the balance is generally understood as the global indication error (slope) measured within the nominal range.
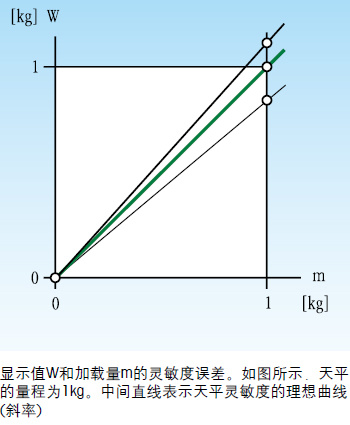
Temperature coefficient of indication error
The indication error depends on the temperature. The degree of dependence is determined by the reversible deviation of the weighing value caused by the temperature change of the environment. This is derived from the temperature coefficient (TC) of the indication error and is consistent with the percentage deviation of the displayed mass (or sample mass) per degree Celsius. For example: when using an XP balance, the temperature coefficient of the indication error is 0.0001% /? C. This means that when the temperature changes by 1 ° C, the indication error changes by 0.0001% or one millionth. The calculation method of temperature coefficient is as follows:
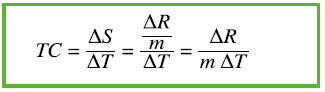
In this equation, ΔS is the change in the indication error and ΔT is the change in temperature. The indicated error change value ΔS is equal to the resulting change value ΔR divided by the load value m or the tare weight of the sample. Using this information, the deviation of the weighing result under certain temperature changes can be calculated by rearranging the above equations. For the displayed value, we can get:

If you weigh the load value (sample mass) of 100g on an XP / XS analytical balance, and the ambient temperature of the laboratory changes by 5 ° C since the last calibration, the following maximum can be obtained in the worst case Result change value ΔR (temperature coefficient of XP is 0.0001% /? C):

If the loading value is only 100mg, that is, a reduction of 1000 times, the maximum deviation will also be reduced accordingly, at 0.5μg.
FACT
Fully Automatic Calibration Technology (FACT).
According to the balance type and linearity, the indication error is automatically corrected. The balance calibration will be triggered whenever the set temperature change value is exceeded.
During the production process of the balance, the internal weights are traceably linked to the international weighing standards through "initial calibration".
In this process, the mass of the internal weight is determined by placing a certified weight on the balance and storing the value in the balance.
proFACT
Professional automatic calibration technology (proFACT). Professional automatic correction of indication error.
Tip: The Excellence Series XP / XS series semi-micro and analytical balances have two sets of built-in weights. This means that during calibration, the balance not only tests the indication error but also the nonlinearity.
Linear (non-linear)
Linearity represents the ability of the balance to follow a linear relationship between the load m and the displayed value W (displayed value error). Here, it is assumed that the ideal curve is a straight line between zero and the maximum load (see: Indication error).
In contrast, nonlinearity defines the width of the frequency band where the positive and negative deviations of the weighing value and the ideal curve occur.
For example: For the Mettler-Toledo Excellence XP analytical balance XP205DR, the maximum deviation from the ideal curve linear process within the entire weighing range of 200g is ± 0.15mg.
Repeatability
Repeatability means that under the same weighing conditions, the balance provides the same result capability when repeatedly weighing a load and the same load ([OIML1) R 76 1] T.4.3).
The same operator must use the same weighing method to perform a series of weighing without interruption at the same position on the same weighing pan, the same installation position, and constant environmental conditions.
The standard deviation of a series of weighings is a way to express repeatability. Especially when using high-resolution balances, the repeatability is not only dependent on the balance performance. Repeatability is also affected by environmental conditions (ventilation, temperature changes, vibration) and samples, as well as the skill of the person performing the weighing operation.
Let us now work together to determine the average and repeatability of this series of weighings.
average value:
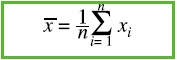
xi = i-th result of this series of weighing
N: Weighing times, usually 10 average
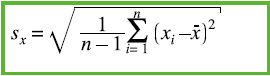
This standard deviation is used as the repeatability reference t. Therefore, the repeatability of this series of measurements is s = 0.0095 mg.
The uncertainty of the weighing result is about two to three times the repeatability u ≈ 2s ... 3s, that is, the actual result x is within the interval x-u <x <x + u. In our weighing, u ≈ 2 s ≈ 2 x 0.01mg = 0.02mg, so that we can get the weighing result by x ± u = 27.51467g ± 0.02mg. Therefore, the minimum weight value of this load predicted by the balance used in the above series of weighing is 27.51465g, and the maximum value is 27.51469g, which is completely consistent with the weighing results of this series.
Traceability
Weighing results ([VIM] 1) 6.10) obtained through a series of uninterrupted comparison chain weighing with specified weighing uncertainty can be traced back to international or national applicable standards. The common weights used for mass weighing can be traced back to the superior standard.
Adjustment level
Set the balance at the reference position of the balance (conventional method: horizontal plane), that is, set its running direction parallel to the vertical direction of the balance. As a rule, this is the same as the horizontal method of setting the balance housing. As a result, distortion will occur due to the cosine of the tilt angle. Corrective measures: All balances offer the option of leveling by using adjustable feet.
Tip: The XP balance of the Beyond Series has: Level Control System. When the balance is not level, LevelControl will automatically issue an alarm and record, which will help improve the reliability of weighing and eliminate the inherent risks of visual control (such as when using weighing instruments).
Partial load
1. The deviation of the weighing value obtained by off-center (eccentric) loading. When the load is loaded and unloaded from the center of the weighing pan, the increase in partial load is related to the quality of the load.
If the same load is placed on different parts of the weighing pan and the displayed value remains the same, it indicates that the balance is off-load. For this reason, when using a high-precision balance, it is important to ensure that the sample is always accurately positioned in the middle.
Reproducibility
Even when weighing individually under the following conditions (specified) according to the following, the degree of similarity between the weighing values ​​of the same weighing variable:
? Weighing process
? Observer
? Weighing instruments
? Weighing position
? Conditions of Use
? Time
Accuracy
A qualitative term for evaluating systematic deviations as a result of symmetric quantities. The closeness of consistency between the predicted value of a series of weighing values ​​and the actual value of the weighed object ([ISO1) 5725] 3.7).
Comment
The accuracy can only be evaluated when there are multiple weighing values ​​and an approved correct reference value.
Accuracy
A qualitative term to evaluate the average deviation as a result of symmetry.
The closeness of consistency between independent weighing values ​​obtained under specified conditions ([ISO1) 5725] 3.12).
The accuracy depends only on the distribution of random errors and has nothing to do with the actual value (accuracy) of the weighing variable.
Examples
The ability of the weighing value provided by the weighing instrument rarely deviates.
Comment
The accuracy can only be evaluated when there are multiple weighing values.
Measurement uncertainty
A parameter that is related to the weighing result and qualitatively determines the dispersion of the weighing value that can be reasonably attributed to the weighing variable ([VIM] 1) 3.9).
This parameter, namely: weighing uncertainty is usually expressed by standard uncertainty u or extended weighing uncertainty U (confidence interval). GUM2) contains instructions on how to determine weighing uncertainty. According to the GUM description, when the secondary errors do not affect each other, the weighing uncertainty is obtained by calculating the sum of the secondary errors.
Comment
There are many ways to calculate weighing uncertainty. For the pharmaceutical industry, it is usually determined in accordance with the United States Pharmacopoeia. Otherwise, the weighing uncertainty is usually determined in accordance with ISO3) 17025. The latter conforms to the GUM method.
Tip: In most countries / regions, METTLER TOLEDO service centers come to customers to perform weighing uncertainty calibration services according to customer needs.
Minimum weight
If it is lower than this value, the relative deviation of the weighing result will be too large.
Tip: METTLER TOLEDO Excellence XP balances provide the most advanced weighing technology and are successfully applied to the weighing of small samples.
calibration
Under the specified weighing conditions, determine the deviation between the weighing value and the true value.
Tip: METTLER TOLEDO Excellence XP and XS balances record and display individual errors on the display, or send them to external software programs or printers.
Correction
Under the specified weighing conditions, determine the deviation between the weighing value and the true value and make corrections.
Sheet Paper,Offset Sheet,Offset Sheet Paper,White Sheet Paper
Puyang Longfeng Paper Co.,Ltd. , https://www.lonfonpaper.com