Perspective soft solvent residue
Editor's note: At present, the problem of exceeding the "benzene content" has caused widespread concern. The residual solvent content of films used in flexible packaging industries such as food, plastic, and pharmaceutical composite packaging has become an unsafe hidden danger due to the residues of benzene, toluene, xylene, butanone, isopropanol, ethyl acetate etc. Solvents are extremely harmful to the human body, especially benzene solvents such as benzene and toluene. Benzene and toluene are colorless liquids with a strong odor. They are extremely toxic and can cause acute poisoning, paralysis of the central nervous system, and other hazards. Therefore, it is necessary to detect the residual solvent amount of the packaging film.
In the process of printing, compounding and coating of composite flexible packaging, a large amount of organic solvents are used, such as toluene, xylene, ethyl acetate, butanone, butyl acetate, ethanol, and isopropyl alcohol. These solvents are more or less left in the composite packaging material. If the packaging material containing the higher residual solvent is used to package foods, drugs, etc., it will endanger people's health.
Therefore, for a composite film using an organic solvent in a composite printing process, the amount of solvent remaining in the composite film should be measured. This issue will discuss the solvent residue problem, detection and control methods in the flexible packaging industry. I hope there will be some reference for my colleagues.
Soft Package Solvent Residues and Process Control
At present, the printing inks and composite adhesives used in the processing of flexible packaging in China contain a certain amount of solvent per se. At the same time, a certain amount of dilution solvent is required to adjust the viscosity during the processing to adapt to the printing composite processing conditions.
(1) Sources of residual solvents
The commonly used dilution solvents for printing inks include toluene, butanone, isopropanol, and xylene. The solvent used in dry composite adhesives is ethyl acetate, and the solvents used in alcohol-soluble adhesives are ethanol and methanol. They are all sources of residual solvents. Although the substrate during printing is passed through a drying system, residual solvents cannot be completely eliminated. Therefore, how to reduce the residual solvent as effectively as possible has become the subject of our research.
(2) Judgment of residual solvent in composite membrane
After the processed composite film is made into a packaging bag, the bag produces an odor, and some films can smell an odor without bag making. To produce this phenomenon, there are generally two situations:
1. Film production; manufacturers add some additives when producing films. After the film is made into Bags , these additives precipitate out of the film and cause odors.
2. Residual solvents in the printing layer and ethyl acetate residue in the packaging are packaged in environmental protection technology. It is caused by too much solvent in the Forum. Before the old, the Russian packaging required quasi-remnants, with a total amount of ≤10mg/m2, and a clear toluene content of ≤3mg/m2. Due to the relatively early formulation of the standard, there was a far cry from this range of requirements and international standards. The United States and Japan require residual solvents ≤ 5mg/m2. China's packaging standards require us to move closer to European and American standards in the future.
(3) Process Control of Solvent Residues
Then need to be controlled in the process, generally in the printing process (1 selection of printing ink, 2 selection and control of diluent, 3 printing machine drying temperature appropriate increase); control of the complex process (1. improve ethyl acetate Purity 2. Curing Room Temperature Control 3. Adhesive Selection 4. Improve Drying Temperature Control System and Exhaust System)
(4) Detection of residual solvent
1. Detection of residual solvent content of packaging materials Using gas chromatograph or equivalent principle instrument, prepare standard solvent samples according to the type of solvent actually used for production, and take 0.5 μl, 1 μl, 2 μl, 3 μl, and 4 μl samples with a microliter syringe, and convert them into quality. The samples were separately injected into a clean and dry 500 ml conical flask sealed with silicone rubber, and placed in a constant temperature oven at 80±2° C. for 30 minutes. Then, 1 ml of gas was taken from the bottle with a 5 ml syringe and rapidly injected into the chromatograph for measurement. According to the total area of ​​its peak value, the standard curve was made with the corresponding sample quality.
2. Ink Solvent Residue Detection Using gas chromatograph or equivalent principle instrument, prepare standard solvent according to the solvent type required by the product standard, and inject 1μl standard into each 300ml infusion bottle through a rubber stopper with 10μl sample injector for each solvent. Solvents were placed in a constant temperature oven at 80±1°C for 20 minutes, then removed and placed in a constant temperature oven at 50±1°C for more than 20 hours every other day. After the removal, 0.2 ml of each solvent was taken from the bottle with a 1 ml syringe. 6, 0.8, 1.0ml gas test, make a standard curve.
Some thoughts on solvent residue in soft film of composite packaging
Control of Residual Solvents in Flexible Packaging Process (1) (2) (3) (4)
Solvent residue detection method
Discussion on Solvent Residual Odor and Solvent Purity Detection of Solvents in Dry Packaging Multi-color Printing Film Solvent(1) (2)
Solvent residual odor and solvent purity detection methods
Discussion on Residual Problems of Compound Packaging Solvent
Problems with Odor and Residual Solvents in Intaglio and Flexo Packaging Printing Fluctuations in Working Viscosity and Effects of Solvent Enrichment on Solvent Residues (Part I) (Part 2)
Study on Performance Test of Low Solvent Residue Composite Adhesive (1) (2)
Analysis of Solvent Residues in Food Compound Soft Packaging
The beautiful, light and inexpensive food composite film packaging bag is one of the stylish and convenient food packaging forms. However, from the smell of milk powder from a well-known domestic enterprise two years ago, the strange smell of pickles and mustards exported from a certain place, to the strange taste of potato chips from a food factory in Gansu Province in recent years, together with the overall qualification of spot checks on food composite film packaging bags. The rate is only 50% or 60%. People's concerns about the safety and health of food composite film packaging bags are not unfounded. The main components of food flexible packaging bags are plastic films, aluminum foils, adhesives and inks. Among them, the film (including aluminum foil) accounts for about 80% of the total composition, the binder accounts for 10%, and the ink accounts for 10%. At present, the adhesives used in domestic packaging materials are mainly based on solvent-based polyurethane adhesives. In developed countries such as Europe and the United States, solvent-based polyurethane adhesives only account for half of the composite adhesives; at home, unless the customer requires the use of Benzene-free ink, otherwise benzene-based ink as the main; in Europe and the United States and other developed countries to benzene-free ink-based. The solvent used for the polyurethane adhesive is ethyl acetate, and the diluent during use is also ethyl acetate (this does not exclude the possibility that individual manufacturers use toluene as a diluent to reduce costs), while the ink contains toluene, butanone, and acetic acid. Ethyl and isopropanol and so on. In order to reduce costs, some manufacturers will use toluene in large quantities. Will these residual solvents be harmful to the human body? How much harm will it cause? How can manufacturers produce a reassuring food composite film packaging bag?
Hygienic Performance Requirements and Residual Solvent Residues for Food Complex Flexible Packaging at Home and Abroad Standards and testing methods. The effects of the compounding process, coating amount, ink, substrate, toluene, water, and adhesives on the solvent residues were systematically analyzed, and the basic process methods and countermeasures for reducing solvent residues were proposed.
Discussion on Solvent Residues in Food Complex Flexible Packaging Bags by Gas Chromatography to Measure Residues in Plastic Food Packaging Bags (1) (2)
Looking at the problem of solvent residue in flexible packaging by the storm of potato chips
Analysis of Solvent Residues in Food Flexible Packaging
Residual Analysis of Residual Chemicals in Food Plastic Packaging Material (I) (II) (III)
Solvent residue in plastic composite flexible packaging
Solvent residue in composite membrane The size of the balance depends on the type of solvent used, the amount of water, the nature of the film substrate used, and the nature of the adhesive. The printing area of ​​the ink and the drying temperature, air volume, production speed, etc.
Rain Boots
Shijiazhuang Mayrain Imp. & Exp. Co. , Ltd. Specializes in rain wears and garments for over 20 years. We make the different style and use of rain boots for different people group. Our products are comfortable, reliable, colorful, and professional. The fabric will be PVC or POLYESTER, it is suitable for people to wear in the rainy day. We have different samples in the Show Room, if you want to know more details about the rain boots, you can click the pic and see the details about them. If there are any problems. Please contact us, the best service will be provided to you always!
Details of Rain Boots
We have a lot of colorful Rain Boot for Child and Adult. The Size are between 149 - 237 mm for kids. The Material is soft PVC or Polyester. Custom logo is available. The MOQ is 1000 pcs per design. Packing details: Each one in per OPP Bag, 12pcs / Ctn. Samples available, Within about 7 working days. Payment term is 30% TT in advance, 70% against BL copy. If requested, our fabric can meet EU Safety Standard and all Plastic material can be AZO Free, Phthalate Free, 6P Free, 10P Free etc. We make three times inspection during the production, the product quality is totally guaranteed. We Shijiazhuang Mayrain Company is a major manufacturer & exporter of Rainwear & Ponchos for more than 20 years.
Our main products are: Adult Raincoat, Promotional Rain Poncho, Kids outdoor Rainwear, waterproof Jacket & other advertising garments. The main fabric of our goods include: PVC, LDPE, EVA, PEVA, Polyester, Nylon & PU with a wide range of high to common quality for various requests.
Our other main products are Kids Raincoat, Adult Raincoat, Kids Poncho, Adult Poncho , Kids Rainsuit , Adult Rainsuit, Kids Smock , Adult Apron , Outdoor Jacket, Workwear , Pants , Sportswear , Gifts & Premium, Promotion , Household Products, bags, Hood , Umbrella , rainboots and Safety Items .
Pictures of Rain Boots:
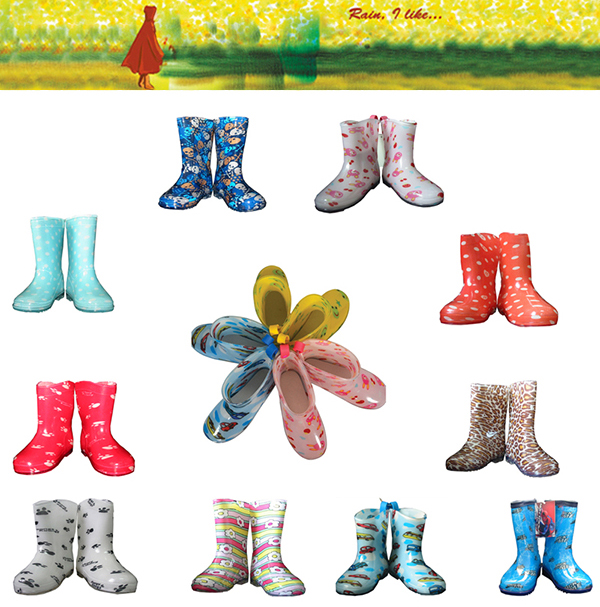
If you are interested in any of them. Please contact us. We will quote you in best price ASAP.
Rain Boots
Pvc Rainboots,Rubber Rainboots,Kids Rain Boots,Plastic Rain Boots
SHIJIAZHUANG MAYRAIN IE CO.,LTD. , http://www.mayraincoat.com