Improvement of the action program of steel barrel seam welder
Improvement of the action program of steel barrel seam welder
Nanjing Yangzi Barrel Factory Zhang Yuanxun
Seam welding is a key process in the barrel production process. According to the requirements of the processing technology, the two ends of the barrel seam welding are leak-welded. The so-called "white head" shall not exceed 3 mm, and "cracking" is not allowed. In this way, the quality of the subsequent crimping (sealing) process can be ensured, and the "triangle area" of the steel drum bead can be ensured without leakage, and a high-quality closed steel drum can be produced.
Strict production process requirements require careful operation by skilled workers, as well as process equipment with precise control and flexibility. Our factory seam welding process uses FN1-150-5 seam welding machine (made in Shanghai). This machine is widely used in steel drum manufacturers. The working principle and operation procedure of the machine mainly include: the disc-shaped switch AJ2 on the foot switch, the J2 normally open contact is closed, the DF1, DF2 electromagnetic valve is energized, the electrode is lowered, the pressure relay is operated, and the pressure switch A1 is connected. , J1 normally open contact closure, turn on the DC motor power supply, the welding wheel rotates, just turn on the controllable silicon inside the control box to make the welding wheel energized and welded. One weld is welded, and the footboard A on the foot switch is stepped on. At this time, J1, J2, DF1, and DF2 are powered off, and the welding wheel is raised (see Figure 1, see the instruction manual for details).
Figure 1 Original electrical principle sketch
Since the seam welding operation is manually manual feeding, the feeding speed and the electrode wheel pressing time are all dependent on the operator's palm. The principle and operation procedure of the FN1-150-5 seam welder requires the operator to hold the barrel tightly with both hands, align the straight seam to be welded with the electrode welding wheel, and step on the foot switch. When the straight seam end enters the center of the welding wheel, immediately press the disc switch A. Time needs to be properly grasped. If it is too early, there will be a “crackâ€; too late, it will “weld the head†and the so-called “whitehead†will appear. Then, to the quasi-direction, the weld must not be twisted and twisted. Solder to the end, the time should be properly controlled, step on the foot switch A to let the welding wheel loosen and rise. If the time is not well mastered, it will also produce "cracks" or "whiteheads", which will burn the welding wheels seriously and cause equipment damage. Therefore, in operation, the operator must use hand, eye, and foot, and use the hand, eye, and foot together to weld the weld that meets the process requirements. The results of our factory practice show. The operational procedures of the equipment, the operation of the workers and the process requirements of the seam welding process are difficult to achieve an effective combination. The pass welding rate of the barrel of our factory is only 20%. Most of the barrels have leakage welding marks and "cracking" phenomenon at both ends, and even several welding wheel sintering accidents occur. That affects the quality of steel drums and affects normal production.
In response to the above problems, we have made corresponding improvements to the working principle and operating procedures of the seam welder. The specific approach is:
1. The electrical control circuit of the seam welder has been improved, and the operating procedures of the equipment operation have been decomposed. Increasing the control welding time of the welding line of the control system is controllable and directly controlled by the operator, which reduces the seam welding defects caused by welding too early or too late. In addition, the limit switch XK is added and installed on the side of the seam welder body. The line is connected in series with the foot switch A. After the seam welding is finished, the power supply is automatically cut off to avoid the loss caused by the pedal operation error.
The action procedure is as follows: see Figure 2.
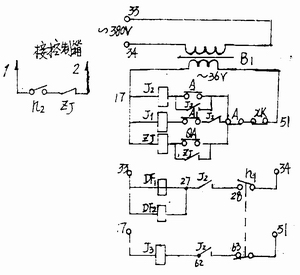
Figure 2 Improved electrical schematic
The barrel is fed into the station, the disc switch A, J2, DF1, DF2 on the foot switch is operated, the pressure switch A1 is energized, the J1 is actuated, the welding wheel is rotated, the optimal starting position is selected, and the button switch QA is pressed. (Installed in the operator's convenient operation position), ZJ relay action, ZJ normally open contact closure, turn on the controllable silicon inside the control box to make the welding wheel energized for welding. When the barrel collides with the limit switch block, XK action, J1, J2, DF1, DF2, ZJ are powered off, the welding wheel rises, and the seam welding is completed.
Figure 3 Schematic diagram of seam welding auxiliary positioning bracket
2. In order to reduce the labor intensity of the manual barrel welding, the stability of the barrel during the seam welding process and the weld seam are straight and smooth. We made a seam-welding auxiliary positioning bracket (Figure 3). Four bearing rollers are installed under the bracket, and the work progresses along the angle steel track with the rotation direction of the welding wheel. Under the support of the operator, the barrel is welded in a straight line at a constant speed. The spring (or elastic tape) under the bracket extends as the bracket advances. When the welding is finished, the limit switch XK moves, the electrode is released, the pressure is released, the spring or elastic tape is contracted, the bracket body automatically returns to the starting station, and the barrel body is turned to the next process.
Our factory has improved the FN1-150-5 seam welding machine to meet the technical requirements of steel drum production. The performance and function of the equipment have been further exerted, which has improved the seam welding quality of steel drums and improved the seam welding workers. The working environment is very popular among workers. In recent years, the pass rate of barrel seam welding in our factory has been maintained at over 99.6%, and we have obtained gratifying benefits.
Paper Gift Box,Paper Box,Pretty Gift Boxes,Square Gift Box
Xing Hua Printing Factory , http://www.xinghuaprint.com